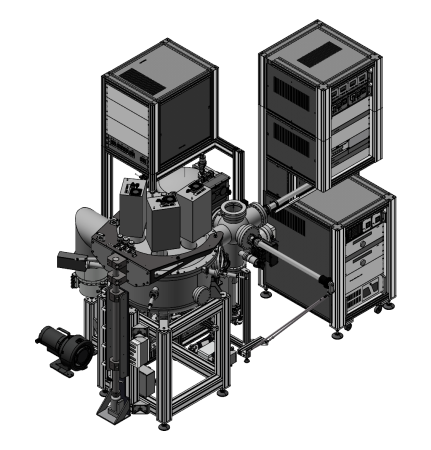
P311+318 – 4″ HV/UHV Multitech. deposition system PDI
Application
Multi chamber system as combination of HV e-beam deposition system & UHV sputter deposition system for thin film and multilayer deposition at 4″ substrates
Year of delivery
2011
Installation site
PDI, Berlin, Germany
Design Features
- Multitechnique deposition system consting a HV E-beam deposition system and a UHV magnetron sputter deposition system connected to a load lock chamber.
- HV E-beam system with combination of two thermal evaporation sources and one multi pocket e-beam source.
- Multi pocket rotary crucible e-beam source (8 pockets with 4ccm each).
- Two thermal evaporation source for standard 3″ and 4″ boat heaters.
- Deposition uniformity better than 2% over 3″ diameter.
- Manually tiltable sample manipulator with integrated sample cooling (without temperature regulation).
- Thickness sensor installed (for rate control and deposition thickness end point detection).
- UHV sputter system with face to face sputtering and sample preparation by ion gun.
- Three 6″ magnetrons installed.
- Deposition uniformity better than 2% over 3″ diameter.
- Three thickness sensors installed (one at each magnetron deposition position for rate control).
- Griddless ion source for sample precleaning and mild etching
- Fully motorized 2 axes sample manipulator (manipulator arm rotation, manipulator z translation) with integrated Bias potential option and sample temperature above 600°C.
- Variable source to sample distance by manipulator z translation.
- Load lock chamber with lamp heating stage.
- Integrated bake out system.
Special Features
- Glace angle depostion possible at e-beam system.
- Reactive deposition possible in both sub-systems.
- Gasflow control via manual dosing valve at e-beam system.
- Gasflow control via MFC at sputtering system.
- Different sample sizes (1″ wafer to 4″ wafer) can be handled (using different clamp connection points of the sample holder).
Outer Dimensions
Technical specifications and performance values
General
Sputtering chamber
Size
About 740 mm diameter, about 780 mm height
Material
stainless steel
E-beam chamber
Size
About 450 mm diameter, about 720 mm height
Material
stainless steel
Load lock chamber
Size
About 150 mm diameter, about 520 mm height
Material
stainless steel
Vacuum
Sputtering chamber
Base pressure
< 3 * 10-9 mbar
Pump down time
1 hour to < 2 * 10-6 mbar
Chamber pumping
Turbo pumping stage, chamber lid differentially pumped by dry foreline pump
Bake out
< 150°C
E-beam chamber
Base pressure
< 5 * 10-7 mbar
Pump down time
1 hour to < 10-6 mbar
Chamber pumping
Turbo pumping stage, chamber door differentially pumped by dry foreline pump
Load lock chamber
Base pressure
< 5 * 10-8 mbar
Pump down time
< 0.5 hours to < 10-6 mbar
Chamber pumping
Turbo pumping stage with dry foreline pump
Manipulator features
Sputtering chamber
Sample size
diameter max. 4″ substrate
Motion axes
2 motorized axes (manipulator arm rotation and z tranlsation of the sample stage)
Temperatures
Room temperature (not stabilized) up to 600°C at sample
Special features
Sample bias (RF, DC or pulsed DC) is possible
E-beam chamber
Sample size
diameter max. 4″ substrate
Motion axes
1 manual axis (manipulator stage tilting)
Special features
3 sample holder clamping positions (one above each deposition source)
Sample preparation features
Sputtering chamber
Oxydation / Nitration /
Plasma treatment
max. 5 * 10-4 mbar partly ionised gas mixture (using a griddless ion gun)
Gas mixture variable from pure argon up to pure oxygen or nitrogen
Ion beam etching /
sample precleaning
Variable ion source to sample distance
Wide range variable ion energy and ion beam current
Load lock chamber
Thermal treatment
Room temperature up to about 300°C at sample (no temperature regulation)